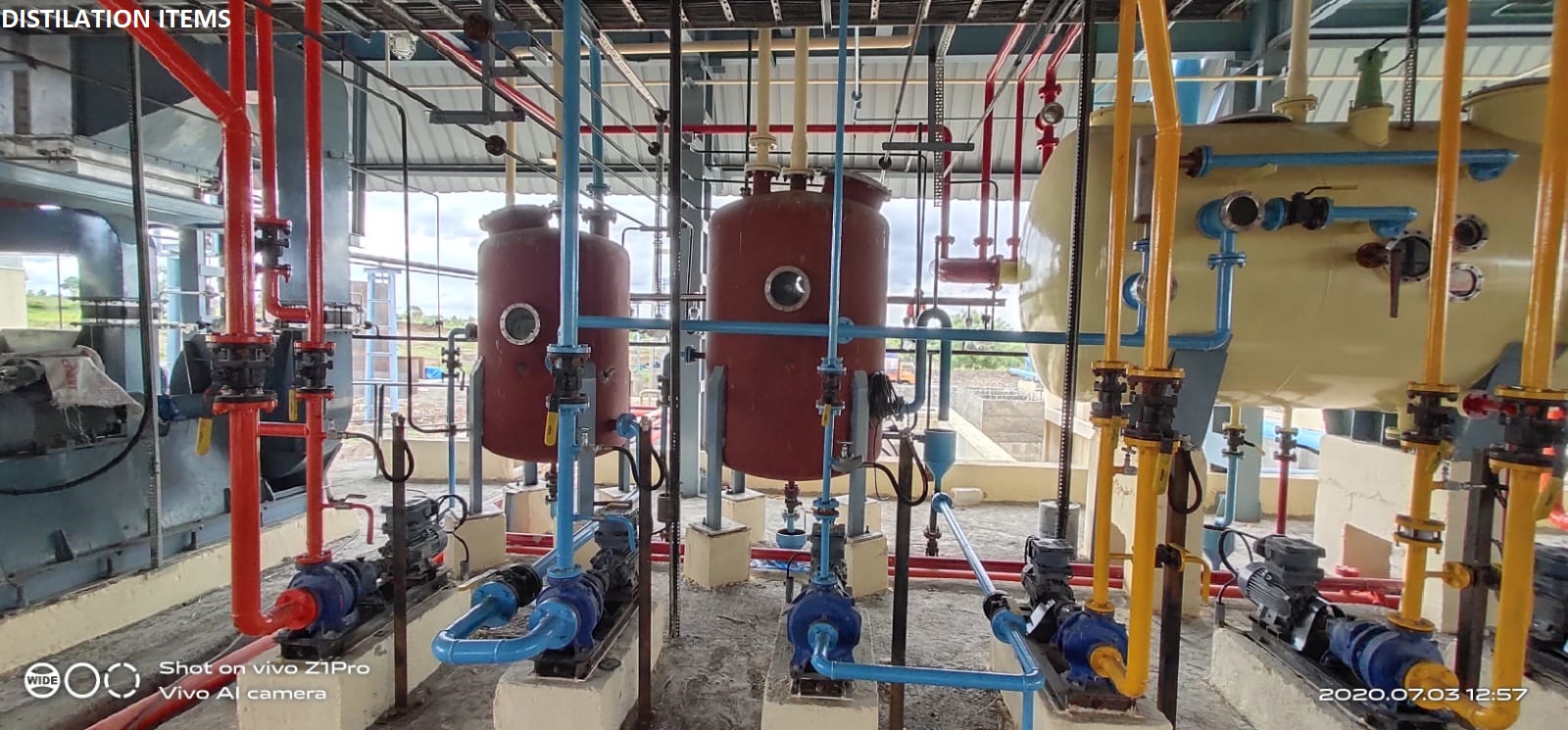

We are committed to understanding their needs
We empower our clients and team members with the knowledge, tools, and support needed to achieve their goals and aspirations.
“Extech Process Engineering” Not only design and supplies plant to its customers but also guides its potential customers to choose the right technology, project and capacity based on feasibility and resource availability from the very first day of interaction. So that the project is successful and the customer can progress.
Once the order is received the following activities are initiated to provide a quality project to the customer as per the industrial requirement, maintaining the project performance guarantee offered by us in our proposal.
- Project Planning
- Detailed Engineering
- Drawing & Designing of the Project
- Sending drawing for manufacturing
- Standardization of product
- Prepared manufacturing schedule for the project to maintain scheduled dispatch time.
- Installation
- Commissioning
- After Sales services
- Providing Layout Plan, Details Drawing, P&ID to our customers for their commissioning readiness
- Quality Check
- In House
- Through Third Party Inspection
- Spares
Installation Supervision
We recognize the fact that installation is very important for successful operation of the plant to achieve the desired output after supply of the plant. To ensure successful commissioning, we depute our most experienced commissioning supervisors/engineers. During their stay at the site, they not only monitor the entire commissioning work, but provide training to the local plant operators /engineers, about the integrity of the plant, functioning of the same and, its functioning and how to handle and resolve any operational.
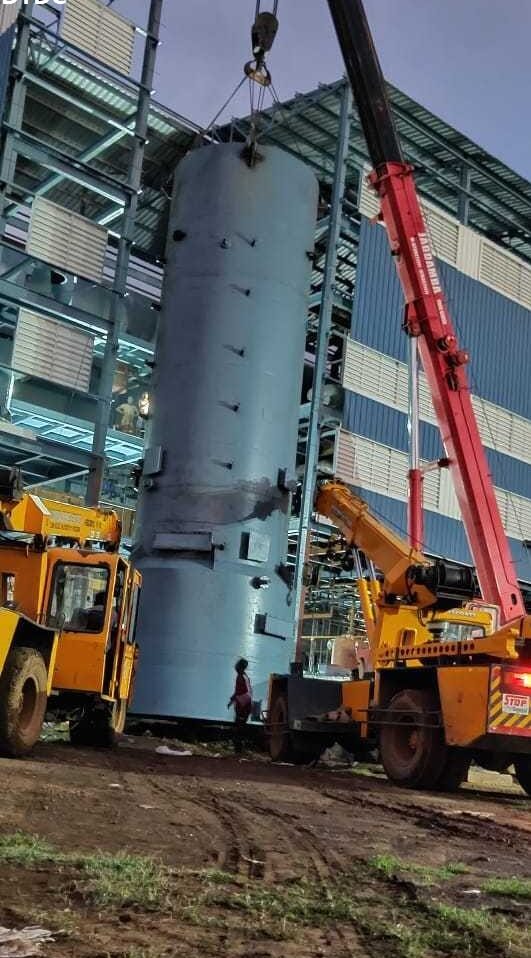
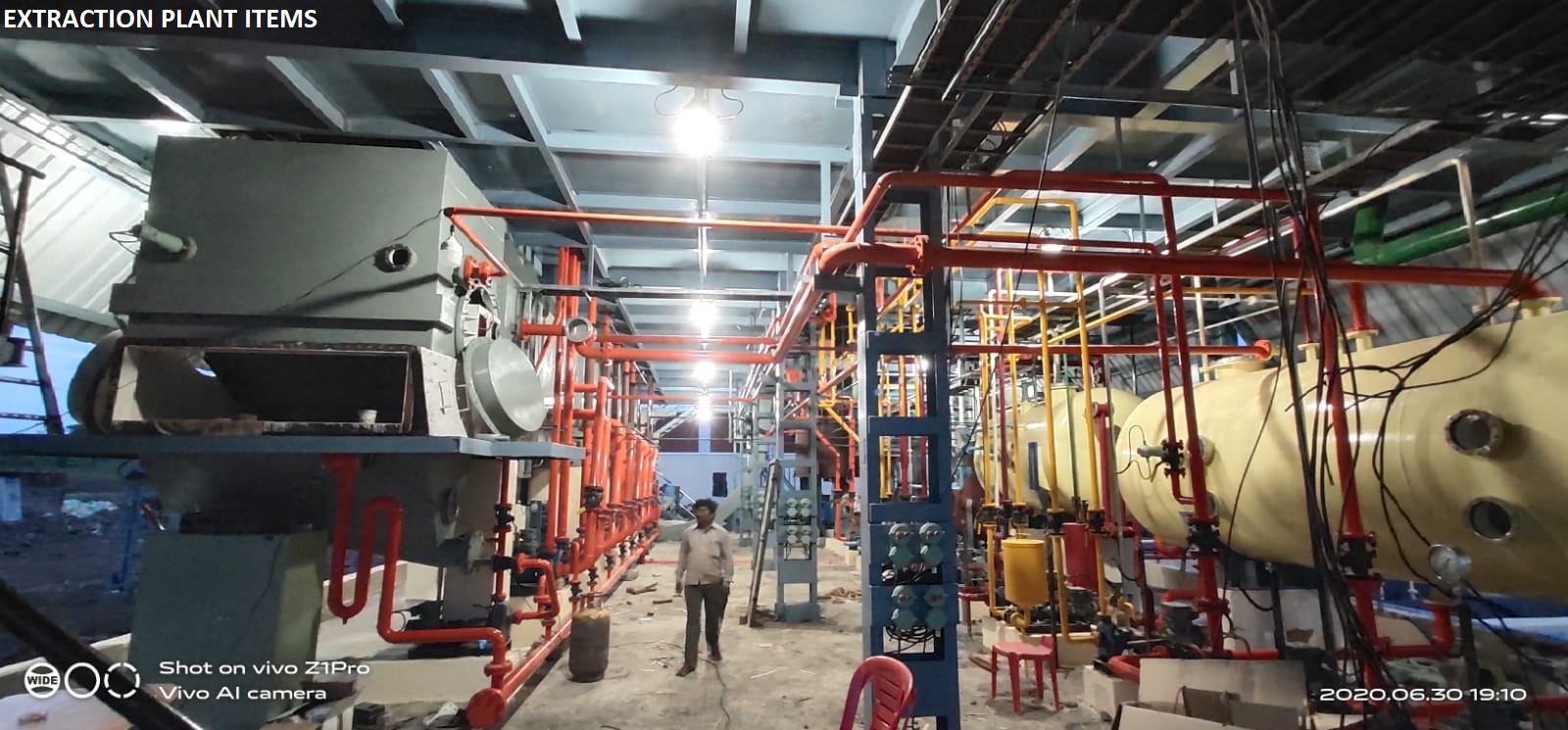
Commissioning Support
After successful installation, under our supervision, our engineers commission the plant, check each and every parameter as per the given guarantee, once they are satisfied with the operation and operating mechanism of the plant, they hand over the plant to our customers. During this, our engineer, in front of the customer and his technical team, runs the plant, shows them that the plant is running, maintains all the operative parameters and finally also shows that the output from the plant is as per the given guarantee.
By us at the time of finalizing the project Once the customer is happy with the operation of the plant and is satisfied with the guarantees received, only then they provide a satisfaction letter to our engineers for the successful commissioning of the plant. On receipt of the letter of satisfaction our engineers leave the site.
Trouble Shooting
Our Service team integrate co-ordination and dovetailing of inputs & resources, towards the prime objectives of shortlisting the key deficiencies in process and equipment, suggesting on the possible corrections / changes in process and equipment to optimise process inputs for extraction and refinery units with the control on cost and quality. Services covered under Trouble shooting Management, include the following:
- Identifying root cause of operation deficiencies.
- Analysing different options to resolve the issues related to production, input cost and product quality.
- Recommending most suited solution to overcome the problems.
- Supervision during implementation of recommendations at the unit.
- Conducting post corrective Quality Audit, monitoring utility inputs to processing and achieving the targeted results based on corrective actions.
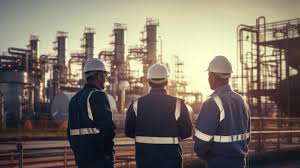
- For Existing Solvent extraction plants, we render our services for followings
- Low utility consumption like hexane, fuel and power.
- End quality improvement of soya meal/ Hi-pro meal / untoasted flakes and extracted oil.
- Minimizing manual interference in process by adopting automation.
- Higher productivity with minimum expenses.
- Value added products.
- For Existing Veg Oil Refinery units, we render our services for followings
- Low utility consumption like chemicals, Bleaching earth, fuel and power.
- End quality improvement of refined oil with high stability.
- Minimizing waste in process by adopting up gradation in process.
- Higher productivity with minimum expenses.
- By products processing for value addition.
- Field staff training for continuous monitoring to control losses in process in terms of products, by products, inputs to process and increasing productivity.